Leaf Blower Manufacturing Plant Project Report | Process, Setup, and Market Trends
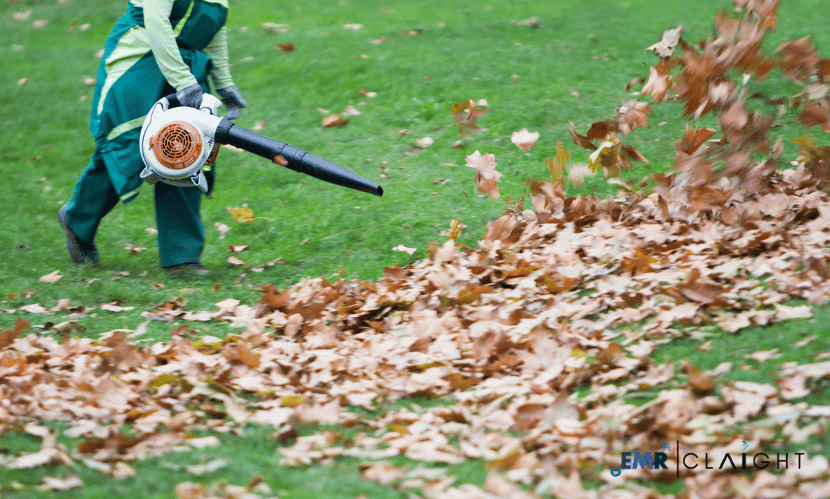
Leaf blowers are essential tools used for clearing debris, leaves, and grass clippings, making them invaluable for landscaping, gardening, and maintenance tasks. With their efficiency and ease of use, leaf blowers have become popular among homeowners, landscapers, and municipal services. As the demand for gardening tools and outdoor power equipment grows globally, establishing a leaf blower manufacturing plant offers a lucrative opportunity to cater to both residential and professional markets.
Overview of the Manufacturing Process
Producing leaf blowers involves a combination of mechanical design, precision engineering, and rigorous quality control to ensure durability and performance.
Key stages in the manufacturing process include:
- Design and Prototyping: Developing ergonomic and efficient designs using CAD software and producing prototypes for testing.
- Component Sourcing: Procuring high-quality materials such as motors, plastic casings, and electronic components from trusted suppliers.
- Motor Assembly: Assembling and calibrating the motor to deliver optimal airflow and performance.
- Casing and Structure: Moulding and assembling the plastic or metal casing that houses the motor and controls.
- Control Systems: Installing user-friendly controls, including speed adjustment and power switches.
- Testing and Calibration: Conducting performance tests to ensure the blowers meet safety and efficiency standards.
- Packaging: Packing the finished product in protective materials with user manuals and warranty information.
Automation in component assembly and testing ensures consistency and efficiency in production.
Get a Free Sample Report with Table of Contents@ https://www.expertmarketresearch.com/prefeasibility-reports/leaf-blower-manufacturing-plant-project-report/requestsample
Plant Setup and Infrastructure
Setting up a leaf blower manufacturing plant requires specialised machinery, skilled labour, and adherence to safety and environmental standards.
Key infrastructure requirements include:
- Assembly Lines: Automated or semi-automated lines for motor assembly and product assembly.
- Injection Moulding Machines: Used for producing plastic casings and other structural components.
- Testing Equipment: Advanced tools for airflow, noise level, and durability testing.
- Storage Facilities: Areas for raw materials and finished products, maintained under optimal conditions.
- Packaging Units: Systems for efficient and secure packaging of leaf blowers.
- Quality Control Labs: Equipped to test for compliance with industry standards and regulations.
Applications and Market Demand
Leaf blowers are versatile tools with applications across various sectors, driving strong demand in both residential and professional markets.
Key applications include:
-
Residential Use:
Homeowners use leaf blowers for yard maintenance and cleaning driveways, patios, and gardens. -
Landscaping Services:
Professional landscapers rely on leaf blowers for efficient cleanup after lawn care and gardening tasks. -
Municipal Maintenance:
Used by municipal services for cleaning public parks, streets, and sidewalks. -
Commercial Spaces:
Employed in commercial properties like shopping centres and office complexes for maintaining outdoor areas. -
Seasonal Cleanup:
Particularly useful in autumn and spring for clearing fallen leaves and debris. -
Specialised Applications:
Modified versions are used in construction sites for cleaning debris and in industrial settings for airflow purposes.
Regulatory and Environmental Considerations
The production and use of leaf blowers require compliance with environmental standards and safety regulations to ensure minimal impact and user safety.
Key considerations include:
- Noise Reduction Compliance: Ensuring products meet noise level limits set by regulatory bodies.
- Emission Standards: Adhering to air quality regulations for fuel-powered models.
- Sustainable Practices: Using energy-efficient machinery and recyclable materials in manufacturing.
- Worker Safety: Providing training and protective equipment for employees handling machinery and chemicals.
- Eco-Friendly Designs: Developing battery-operated or electric models to reduce emissions and environmental impact.
Cost Factors and Investment
Setting up a leaf blower manufacturing plant involves costs related to infrastructure, equipment, raw materials, and operational expenses. Investments in research and development, marketing, and certifications are crucial to gaining a competitive edge in the outdoor power equipment market.
Conducting a feasibility study helps assess market potential, resource allocation, and operational challenges. Collaborating with suppliers and technology partners can streamline production and improve efficiency.
Features of a Modern Manufacturing Facility
Modern facilities for leaf blower production integrate advanced technologies and sustainable practices to ensure efficiency and quality.
Key features include:
- Automation: Enhances production speed and ensures consistent product quality.
- Energy Efficiency: Utilises energy-saving equipment to minimise operational costs and environmental footprint.
- Real-Time Monitoring: Tracks production metrics to optimise efficiency and detect potential issues early.
- Sustainability Practices: Focuses on waste reduction and eco-friendly packaging solutions.
- Scalability: Designed to accommodate future expansions and meet growing market demand.
Challenges and Opportunities
The leaf blower market offers significant growth potential but also presents certain challenges:
- Market Competition: Competing with established brands requires innovative features and strong branding.
- Raw Material Costs: Fluctuations in the prices of motors and plastics can affect production costs.
- Consumer Awareness: Educating consumers about the benefits of newer, eco-friendly models can drive adoption.
Opportunities include expanding into emerging markets, developing smart or IoT-enabled leaf blowers, and focusing on battery-operated models for eco-conscious consumers. Leveraging e-commerce platforms and partnerships with landscaping companies can further enhance market presence.
Operational Best Practices
Efficient operations are critical for the success of a leaf blower manufacturing plant. Recommended practices include:
- Routine Maintenance: Keeps machinery in optimal condition, reducing downtime.
- Employee Training: Equips workers with skills to handle advanced equipment and maintain safety standards.
- Quality Assurance: Implements stringent testing to ensure product reliability and compliance with safety standards.
- Inventory Management: Balances raw material procurement with finished product demand effectively.
Future Prospects
The demand for leaf blowers is expected to grow as consumers and professionals seek efficient and convenient outdoor cleaning solutions. Manufacturers focusing on innovation, sustainability, and user-friendly designs will be well-positioned to capture this growth and establish a strong presence in the outdoor power equipment market.
Establishing a leaf blower manufacturing plant presents a lucrative opportunity to meet the rising demand for high-performance, eco-friendly outdoor cleaning tools while contributing to advancements in landscaping and maintenance technology.
- Local News
- World News
- Crime
- Politik
- Film
- FootBall
- Food
- Games
- Health
- Home
- Literature
- Music
- Networking
- Other
- Religion
- Shopping
- Sports
- Opinion
- Tech
- Scam
- Bussines News
- Credit
- Hosting
- Insurance
- Infomation
- Finance
- Entertaiment
- Education
- Artist
- Trick and hack
- Forex
- Review
- Vps Forex
- Cerita
- agriculture
- assistance
